Five common shoe defects and solutions
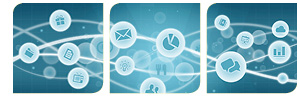
Footwear manufacturing is a complex process that spans many stages, from design and material selection to assembly and finishing. Ensuring high quality in the final product is a crucial aspect of this process, as it directly affects customer satisfaction and brand reputation.
Each year we help different retailers and buyers in running on-site quality control of their footwear before shipment. In this article, we have gathered findings and insights from our inspection team on common footwear quality issues and possible solutions to improve quality performance.
Material defects
Material defects are responsible for many issues in footwear manufacturing, affecting natural or synthetic leather and textiles, for example. We often encounter visible defects, such as scars, holes, scratches, stains and discoloration, which can significantly affect the final product's aesthetics and quality, and in most cases are regarded as major defects.
Unwanted pattern on leather |
Damaged leather |
![]() |
![]() |
Solution: To mitigate this issue, manufacturers should conduct stringent quality controls during the sourcing and selection of raw materials. Incoming quality control is often used to check the conformance of raw materials and other materials before production begins.
In addition, a proper handling process for internal materials and semi-finished components is required, as most defects arise during the manufacturing/assembly process. Materials and semi-finished components are often damaged during transportation and storage, therefore appropriate management of the storage environment, e.g. humidity, is an effective way to avoid deformation and defects between manufacturing processes. This is particularly crucial before critical or high-risk production processes take place, as the rework/repair cost of finished goods is much higher than semi-finished goods.
As real leather is a natural material, it is imperfect by nature. Leather usability assessments can be conducted before manufacturing to more precisely identify and predict if this important material is fit for purpose.
Adhesive or cementing failure
Footwear manufacturing frequently uses adhesives to bond components, such as soles, uppers, insoles and accessories. Adhesive and cementing failure can result in structural issues, causing the shoe to fall apart and posing a significant quality problem.
Overflowing of glues, glue marks and inadequate cementing are common visual symptoms of this issue. While the first two are usually considered minor defects, cementing failure is considered to be major.
Excess glue |
Glue mark |
|
|
Cementing failure |
|
|
Solution: To prevent adhesive failures, first and foremost, manufacturers should carefully select the appropriate adhesives for the materials used. Adhesives should be handled and stored properly to ensure their bonding functionality. If in doubt, adhesive strength tests can be performed before production takes place.
Using expired glues can also be an underlying cause. Expired glues lose their ability to bond, thereby causing cementing failure. Glue suppliers should provide such product information with the glue, and this should be marked clearly on each glue container at working stations. Regularly checking expiry dates as part of the quality assurance/control process is a very helpful way to avoid problems.
Adhesive or cementing problems are also closely related to workmanship, which can be improved by process standardisation and training workers on key topics such as surface preparation, application method, and glue cleaning skills. The application method instructions should contain clear information on application tools, amount of adhesive, time needed, and the required pressure and temperature. Despite these measures, inline quality checks are still required to make sure there are no errors and that quality is consistent across all production lines and stations.
Poor finishing
Footwear finishing impacts the final product's appearance and sometimes the shoe’s fit, reducing the sellable value of the goods. Poor finishing includes rough edges, asymmetric properties, and uneven trimming, often considered major defects.
Height deviation |
Slanted shoe body |
![]() |
![]() |
Wrinkle marks |
Faulty stitching |
![]() |
![]() |
Solution: It is essential that workers have comprehensive training on how to produce high-quality footwear, as footwear production involves many complex manual steps. This concerns not only the shoe construction line but also the upper construction, sole construction, finishing and packing lines.
Upon receiving a new order, machines should be calibrated and workers prepared for the requirements of the order. Any gaps identified during calibration should be fixed to minimise the risk of production issues at a later stage. For some factories, technical audits are conducted as a systematic assessment of capabilities and capacities so that improvements can be plotted out more effectively.
Metal and sharp points
Metal and sharp points are relatively uncommon footwear issues that pose a significant risk to consumers. Exposed metal wares due to poor assembly, or loosened metal components, could lead to sharp edges. In extreme cases, metal components are accidentally left inside of shoes.
Loose eyelet |
Sharp steel shank without protection |
![]() ![]() |
![]() |
Nail inside shoe |
|
![]() |
Solution: Unlike garment and textiles goods, metal detection machines are not usually the best solution, as many shoes contain metal as construction support or design elements. The machine can, however, be used on individual components such as uppers and insoles to check for unintended metal.
The more reliable way to control this hazard is through stringent control of broken needles and sharp points on the production line. Checking metal components such as eyelets, buckles and trims for sharp point or edges should be carried out during final random inspection (FRI).
A workforce training on “Needle and Hazardous Metal Detection Policy/Procedure” and “Sharp Object Management” is essential so that workers can undertake the control process systematically and with due care.
Inconsistent sizing and fit
Inconsistent sizing and fit can stem from various factors, such as inaccurate moulds or patterns, machine calibration errors, or assembly inconsistencies and errors. Shoes that do not comply with standard sizes and fits will no doubt lead to customer dissatisfaction and increased return rates.
Wrong size packing |
|
Solution: A thorough quality control process at multiple stages of the production is a great solution to managing sizing and fit issues, whether in-house or by a third-party. As well as product quality inspection, an ideal process should include tools monitoring, equipment calibration, inline/batch review, worker capability development, proper documentation and on-going monitoring procedures, from material sourcing to shipping.
Although the footwear manufacturing industry faces various quality challenges, a good awareness and proactive implementation of the solutions discussed above can greatly mitigate any issues. By prioritising quality control, improving material selection, adhering to standardised procedures, and investing in employee training, manufacturers can maintain stable quality and reduce costs in the long run.
Eurofins has strong expertise in footwear inspection. Contact us for a solution customised to your needs!
CLICK HERE TO SEND YOUR REQUEST
Or contact us now to receive consulting and testing services for your product
Eurofins Consumer Product Testing Vietnam
- Address: 1/4 Tan Thoi Nhat 18 Street, Tan Thoi Nhat Ward, District 12, Ho Chi Minh City, Vietnam.
- Hotline: +84 28 7109 8828 (Ext: 117, 119, 128)
- Email: CPTVNsales@cpt.eurofinsasia.com